Pilotní jednotka využívající BRO pro výrobu biomethanu (RNG) katalytickou methanizací
Katalytickou methanizací oxidu uhličitého se zvyšuje obsah udržitelného biomethanu, respektive RNG (Renewable natural gas), vyrobeného z BRO (biologicky rozložitelného odpadu). Výhodou je produkce biomethanu (zvýšení obsahu energie) bez nutnosti separace oxidu uhličitého.
Zveřejněno se souhlasem Českého plynárenského svazu, vydavatele časopisu Plyn, sešit 2-2023.
Souhrn
Článek se zabývá využitím tzv. Sabatierovy reakce neboli katalytické methanizace oxidu uhličitého jako alternativního způsobu výroby udržitelného biomethanu, respektive RNG (Renewable natural gas), vyrobeného z BRO (biologicky rozložitelného odpadu). Výhoda katalytické methanizace oproti běžně využívaným metodám pro zušlechťování bioplynu je produkce biomethanu, resp. RNG bez nutnosti separace oxidu uhličitého. Oxid uhličitý v bioplynu je pomocí katalytické methanizace efektivně přeměněn na methan. V současné době je bioplyn zušlechťován na biomethan výhradně separací oxidu uhličitého. Velkou nevýhodou těchto metod je produkce oxidu uhličitého, který je dnes nejčastěji vypouštěn do ovzduší, což přispívá ke zvyšování jeho koncentrace v atmosféře. Naproti tomu mezi výhody katalytické methanizace patří nízká spotřeba elektrické energie samotného procesu methanizace a možnost využití vznikajícího vysokopotenciálního tepla. Odváděné teplo může být využito například pro ohřev fermentorů, ve kterých vzniká bioplyn. Z těchto důvodů lze předpokládat budoucí využití katalytické methanizace jako alternativního způsobu zušlechťování bioplynu.
Summary
The contribution discusses the use of the Sabatier reaction, i.e., catalytic reduction of carbon dioxide to methane (catalytic methanation), as an alternative method for producing sustainable biomethane, or RNG (renewable natural gas), produced from BDW (biodegradable waste). Compared with the methods that are normally employed for biogas upgrading, the advantage of catalytic methanation is that biomethane, or RNG, is produced without the need to separate carbon dioxide. Catalytic methanation effectively transforms carbon dioxide in biogas into methane. Biogas is currently upgraded to biomethane solely by carbon dioxide separation. A major downside of these methods is that carbon dioxide is being produced in the process, and most frequently released into the air, which contributes to its levels in the atmosphere rising. On the other hand, the benefits of catalytic methanation include low consumption of electrical energy in the actual methanation process and an opportunity to use the high-potential heat generated in the process. The dissipated heat can, for example, be used for heating the fermentation tanks in which biogas is produced. Catalytic methanation can therefore be expected to be employed in the future as an alternative method for biogas upgrading.
Úvod
Bioplyn hraje klíčovou roli na trhu s obnovitelnou energií. V České republice se v roce 2021 podílel třemi procenty na celkové výrobě elektrické energie [1]. V současné době jsou technologie na přeměnu biomasy pomocí anaerobní fermentace známé a využívané v širokém měřítku. V České republice je provozováno 579 bioplynových stanic [10]. Bioplyn se skládá převážně z methanu a oxidu uhličitého. Použitá biomasa a technologie může ovlivnit složení surového bioplynu. Majoritními složkami jsou methan (45–75 obj. %) a oxid uhličitý (25–48 obj. %). Bioplyn dále obsahuje minoritní složky, jakou jsou sirné sloučeniny, tvořené převážně sulfanem (0–3 obj. %), kyslík (0–1 obj. %), dusík (1–3 obj. %), vodík (0–3 obj. %), oxid uhelnatý (0–1 obj. %) a amoniak (stopové množství). Hlavním problémem pro širší nasazení bioplynu je právě jeho složení. Některé z nečistot (CO2, NH3, H2S) mají významný negativní vliv nejen na lidské zdraví, ale také způsobují problémy při následném energetickém využití bioplynu [2, 4]. V současné době se nejčastěji využívá v kogeneračních (příp. trigeneračních) jednotkách, které vyrábí elektrickou energii a teplo, příp. i chlad. Současně vyráběné teplo se však často nevyužívá, čímž dochází k maření části energie obsažené v bioplynu. Nejen z tohoto důvodu dochází k širšímu nasazování technologií na zušlechťování bioplynu na biomethan.
V Evropě je již více než 1 000 biomethanových stanic [5]. Přibližně 10 % z nich není připojeno k plynárenské síti a produkovaný biomethan využívají pro své účely nebo mají například v areálu biomethanové stanice plnicí stanici CNG. Aktuálně jsou v České republice provozovány 3 biomethanové stanice, jedna v Rapotíně u Šumperku, druhá v Litomyšli a třetí se nachází v Horní Suché na Karvinsku [9]. Nejrozšířenějšími technologiemi pro zušlechťování bioplynu jsou dnes především membránová separace, proces tlakové adsorpce (PSA – Pressure swing adsorption) nebo chemická či fyzikální absorpce pracím roztokem. Společná nevýhoda výše zmíněných technologií je především neřešení problému, co s odpadním oxidem uhličitým, který je často znečištěn methanem. Z tohoto důvodu se nabízí využití katalytické methanizace jako alternativní technologie pro zušlechťování bioplynu. Využití katalytické methanizace bioplynu přináší řadu výhod jako například produkci biomethanu (RNG – Renewable natural gas) bez odpadního oxidu uhličitého, možnosti využití odpadního tepla produkovaného methanizační reakcí například pro vytápění fermentorů, vyšší produkce biomethanu (RNG) než konvenční technologie (CO2 z bioplynu se využívá pro produkci RNG) a v neposlední řadě nám umožnuje stabilizovat elektrickou síť díky použití elektrolyzéru pro výrobu potřebného vodíku pro metanizační reakci [3, 4].
Výroba bioplynu a biomethanu
Výroba bioplynu
Bioplyn je produkován anaerobním rozkladem organických látek jako je BRO (biologicky rozložitelný odpad), BRKO (biologicky rozložitelný komunální odpad), kejda, čistírenský kal nebo energetické plodiny. Hlavními složkami bioplynu jsou methan a oxid uhličitý. Dále se v bioplynu nejčastěji vyskytuje vodík, dusík, kyslík, sulfan a amoniak. Při anaerobním rozkladu biomasy zůstává ve fermentoru nerozložený zbytek organických látek, který je pro prostředí nezávadný [6].
Bioplyn je obnovitelný zdroj energie, který může být využit jako náhrada fosilních paliv. Při jeho výrobě vzniká vysoce kvalitní digestát, které se může využít například pro výrobu hnojiv. V neposlední řadě výroba a využití bioplynu podporuje lokální ekonomiku a snižuje závislost na importu energetických surovin, čímž zvyšuje energetickou soběstačnost. V současné době je stále nejvíce bioplyn využíván pro kombinovanou výrobu elektrické energie a tepla, případně chladu. Tento způsob využití bioplynu je často neefektivní, protože zejména v teplejších měsících je produkovaná tepelná energie mařena, což výrazně snižuje účinnost celého systému. Bioplyn se také využívá jako palivo pro získávání tepla a v posledních letech je stále častěji využíván pro produkci biomethanu [6].
Výroba biomethanu
Zušlechťování bioplynu je proces, který zvyšuje výhřevnost bioplynu. Snižuje jeho relativní hustotu a umožňuje širší využití bioplynu. V současné době je v Evropě více než 1 000 biomethanových stanic, přibližně 47 % z nich vtláčí biomethan do distribuční sítě, 20 % do přepravní sítě, 10 % není připojeno a biomethan například využívá ve svém areálu pro CNG stanice a o zbylých cca 23 % biomethanových stanic nejsou informace dostupné [5].
Bioplyn má velice malou míru využitelnosti, hlavně kvůli jeho složení, které znemožňuje širší uplatnění tohoto energetického plynu. Jednou z nevýhod bioplynu je jeho nízká výhřevnost oproti běžně využívanému zemnímu plynu. Další nevýhodou je produkce většího množství emisí škodlivých látek při jeho spalování než při využití paliv vyšší generace. V neposlední řade můžou jeho minoritní složky, zejména sulfan, amoniak, oxid uhličitý a oxid uhelnatý způsobovat korozi energetických zařízení využívající bioplyn. Z uvedených důvodů se nabízí zušlechťování bioplynu jako vhodná technologie pro produkci paliva s vyšší přidanou hodnotou, které může využít i širší veřejnost [4, 6].
Výroba biometanu probíhá ve více krocích. V prvním kroku se surový bioplyn zbaví nežádoucích látek, jako je např. sulfan a amoniak. Poté se vysuší a následně je z něj odseparován oxid uhličitý pomocí jedné ze zušlechťovacích metod. Mezi konvenční metody patří fyzikální absorpce (např. vodní vypírka, proces Rectisol nebo Selexol), chemická absorpce (např. aminová vypírka), tlaková adsorpce (např. PSA nebo VPSA), kryogenní separace a v posledních letech nejčastěji nasazovaná membránová separace. Alternativně lze využít přímou methanizaci bioplynu. Zušlechtěný bioplyn se nazývá biomethan, respektive při využití methanizace RNG. Biomethan, resp. RNG zvyšují využitelnost bioplynu a umožnují jeho využití i širší veřejnosti. Kvalita biomethanu, resp. RNG odpovídá legislativním požadavkům, případně požadavkům provozovatele plynárenské infrastruktury, do které je biomethan (RNG) vtláčen [3, 4].
Katalytická methanizace bioplynu
Katalytická methanizace je především známá jako součást konceptu Power-to-Gas, ve kterém se přeměňuje vyráběný vodík z obnovitelných zdrojů na RNG a díky tomu může být využito již vystavěných distribučních i skladovacích kapacit plynárenské infrastruktury. Takto vyrobený RNG má stejné vlastnosti i využití jako těžený zemní plyn. Katalytická methanizace je reakce vodíku a oxidu uhličitého za vzniku methanu, vody a tepla. Vodík potřebný pro reakci je vyráběn pomocí elektrolýzy vody z elektrické energie dodávané obnovitelnými zdroji, jakou jsou například fotovoltaické a větrné elektrárny. Oxid uhličitý potřebný pro methanizační reakci se může získávat ze spalin fosilních elektráren, průmyslových procesů, ze vzduchu a v neposlední řadě z bioplynu [3].
Bioplyn se jeví jako perspektivní zdroj oxidu uhličitého pro methanizační reakci kvůli svému složení. Oxid uhličitý obsažený v bioplynu je potřebný pro methanizační reakci a přítomný methan je produktem methanizace. Při využití bioplynu jako zdroje oxidu uhličitého můžeme mluvit o katalytické methanizaci jako alternativní metodě zušlechťování bioplynu. Hlavní výhodou katalytické methanizace je produkce RNG bez nutnosti separace oxidu uhličitého. Další nespornou výhodou je vyšší (až dvojnásobná) produkce RNG, protože oxidu uhličitý přítomný v bioplynu se neodstraňuje, ale využívá pro výrobu RNG. Katalytická methanizace také pomáhá se stabilizací elektrické sítě, může ukládat přebytky elektrické energie do RNG a pomáhá s vykrýváním odběrových špiček. V neposlední řadě může být využito odpadní vysokopotenciální teplo, které vzniká samostatnou methanizační reakcí. Toto teplo je nutné z methanizačního reaktoru odvádět, aby nedošlo k přehřátí katalytického lože a tím k jeho sintraci, což by vedlo k nevratné deaktivaci katalyzátoru. Odpadní vysokopotenciální teplo může být využito například pro ohřev fermentorů, ve kterých se produkuje bioplyn, případně může být distribuováno ke koncovým zákazníkům (domácnosti, školy atd.).
Methanizační reakce probíhá v rozmezí teplot od 180–550 °C v závislosti na použitém katalyzátoru. Nejčastěji jsou využívány katalyzátory na bázi niklu, které jsou relativně levné a disponují vysokou katalytickou aktivitou a selektivou na methan. Tyto katalyzátory běžně disponují více než 90% konverzí oxidu uhličitého. Nevýhodou niklových katalyzátorů je především jejich velice nízká odolnost na sirné látky, které způsobují jejich nevratnou deaktivaci. Proto musí být vstupující bioplyn do methanizační jednotky odsířen [7].
Pro snížení ceny, zajištění stability katalyzátoru a zvýšení katalytické účinnosti se využívají takzvané nosiče katalyzátorů. Nosiče umožnují snížit množství použitého katalytického kovu, při zachování dostatečného specifického povrchu, který je důležitý pro methanizační reakci. Za nejvyužívanější nosiče katalytických kovů pro methanizační reakci se považují nosiče na bázi keramiky: Al2O3, TiO2, SiO2, ZrO2 a CeO2 [7].
Vývoj pilotní jednotky na výrobu RNG z BRO
Pilotní jednotka produkující RNG z BRO
V rámci projektu „Vývoj zařízení maximalizující využití BRO při přeměně na bioplyn s využitím katalyzátoru na konverzi CO2 a následného termochemického zpracování odpadního materiálu“ je vyvíjena pilotní jednotka pro výrobu obnovitelného zemního plynu (RNG) z biologicky rozložitelného odpadu (BRO), především z čistírenských kalů a gastroodpadu (respektive jedlých olejů a tuků). Dnes jsou technologie na přeměnu BRO známé a využívané v širokém měřítku. Zvýšené využívání těchto technologií přináší i zvýšení produkce odpadního oxidu uhličitého a problémy spojené s výsledným produktem anaerobní fermentace, kdy výsledný produkt při zhoršených vlastnostech (parametrech) vstupního produktu vykazuje zvýšené rizikové faktory (obsah rizikových látek a patogenů). S takovýmto odpadem je nutné dále nakládat, což sebou nese zvýšené energetické a materiálové nároky. Vyvíjená pilotní jednotka tyto nedostatky odstraňuje.
Výhodou vyvíjeného zařízení je komplexní řešení pro nakládání s odpadem i vyvinutým bioplynem. Pilotní jednotka zajištuje energetické využití BRO a následné termochemické zpracování odpadního produktu z anaerobní fermentace, při kterém je zbaven nebezpečných vlastností, respektive legislativou stanovených limitů na obsah rizikových látek a patogenních organismů. Konečné termochemické zpracování odpadu je odpovědí na komplexní úpravu BRO (hygienizace, sušení a pražení). Produkovaný bioplyn je vyčištěn a převeden pomocí katalytické methanizace na RNG. Následně RNG uložený v zásobníku je využit buď pro termochemickou úpravu odpadu a vtlačení přebytků do plynárenské sítě, anebo využit lokálně pro účely bioplynové stanice. Dále jednotka disponuje využitím odpadního tepla z katalytické methanizace pro termochemickou úpravu odpadního produktu, čímž se snižuje spotřeba RNG.
Obr. 9 zobrazuje zjednodušené schéma vyvíjené pilotní jednotky. V prvním kroku dojde k přečerpání BRO do fermentačního reaktoru, kde dochází k tvorbě bioplynu a částečné stabilizaci BRO. Vyvinutý bioplyn je následně ukládán do vaku, ve kterém je skladován při mírném přetlaku oproti atmosféře. Dalším krokem je úprava bioplynu pro využití v methanizační jednotce a jeho následné uskladnění v zásobníku upraveného bioplynu při tlaku 35 bar (pracovní rozsah zásobníku 6–35 bar). Upravený bioplyn je následně redukován na cca 5 barů a je veden do methanizační jednotky, kde je přimícháván ve zvoleném poměru k vodíku, vyráběného pomocí PEM elektrolyzéru. Tato směs je dále vedena přes výměník tepla a předehřev plynu do reaktoru, ve kterém je uložen katalyzátor a kde probíhá samotná methanizační reakce. Z reaktoru je produkovaný plyn veden přes výměník tepla (předehřátí vstupního plynu), chladič (dochlazení plynu na teplotu pod 50 °C) až k odlučovači kondenzátu (odloučení reakční vody). Produkt zbavený reakční vody je následně on-line analyzován a ukládán do zásobníku pro další využití. Finální odpad z anaerobního fermentoru je následně termochemicky stabilizován.
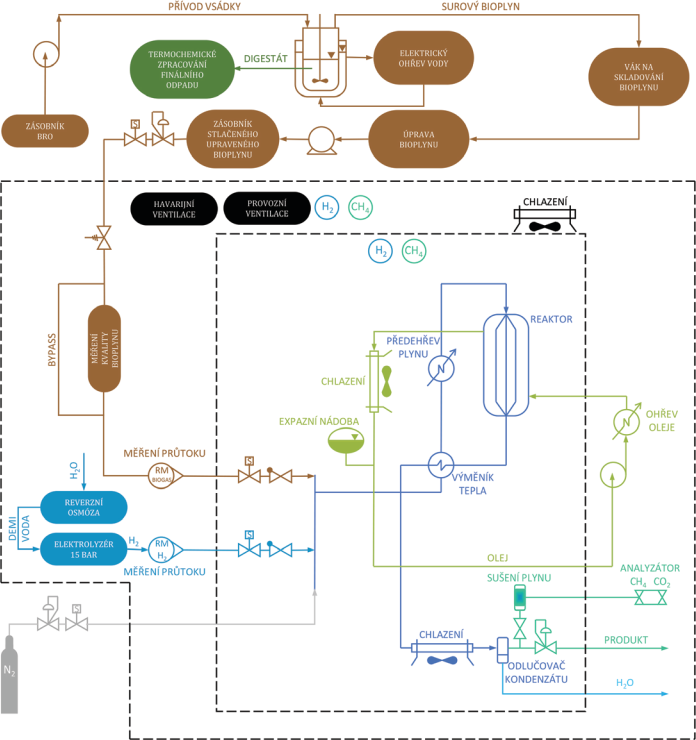
Obr. 9 Zjednodušené schéma pilotní jednotky pro výrobu RNG z BRO
Na vyvíjeném zařízení spolupracuje konsorcium ÚJV Řež, a. s., Mendelova univerzita v Brně a VIA ALTA a. s. ÚJV Řež má na starost primárně vývoj methanizačního zařízení a katalyzátoru pro výrobu RNG z BRO. Dále spolupracuje na optimalizaci čištění bioplynu pro jeho využití v methanizační jednotce – primárně odstranění katalytických jedů a dále minoritních látek, které musí být odseparovány kvůli legislativním požadavkům na výslednou kvalitu produkovaného RNG.
Vývoj katalyzátoru pro methanizační jednotku
V rámci projektu bylo v ÚJV Řež postaveno testovací zařízení, na kterém probíhal vývoj katalyzátoru a dále se zde testovaly části vyvíjené pilotní jednotky. Schéma testovacího zařízení je obdobné jako na zjednodušeném schématu pilotní jednotky (obr. 9 – část ohraničená přerušovanou čarou).
Pro methanizační reakci byl zvolen katalyzátor na bázi niklu charakteristický vysokou katalytickou aktivitou a selektivitou na methan a příznivou cenou mezi katalytickými prvky. Jako jeho nosič byl zvolen směsný nosič na bázi Al2O3 a CeO2. Al2O3 je levným a vyzkoušeným nosičem pro methanizační reakci a CeO2 zvyšuje stabilitu nosiče a podporuje i samotnou methanizační reakci. Nosič byl na základě know-how ÚJV Řež vyroben firmou EuroSupport s.r.o, kde jeho složení je 25 hm. % CeO2 a zbytek je tvořen Al2O3. Následně byl na tento nosič několikanásobně naimpregnován dusičnan nikelnatý. Finální zatížení katalyzátoru niklem bylo stanoveno (XRF) na 49,5 hm. %.
Pracovní přetlak | 5–15 bar |
Teplota chladícího oleje | max. 320 °C |
Teplota v reaktoru | max. 600 °C |
Maximální produkce vodíku | 1 Nm3/h |
Využívání modelový bioplyn | 30–70 obj. % methanu |
Testování katalyzátoru Ni/CeO2-Al2O3
Pro testování katalyzátoru byla použita testovací methanizační jednotka. Nejprve bylo do reaktoru umístěno 250 ml katalyzátoru. Následně byl celý systém methanizační jednotky natlakován dusíkem na 5 bar, aby mohla být provedena zkouška těsnosti systému. Po dokončení tlakové zkoušky byl do reaktoru puštěn vodík a reaktor byl postupně ohříván na teplotu cca 300 °C, aby došlo k redukci oxidu nikelnatého na nikl (aktivace katalyzátoru). Po cca 24 hodinách byla ukončena redukce katalyzátoru. Po dalších cca 24 hodinách v atmosféře vodíku a při teplotě okolí byla ukončena aktivace katalyzátoru. Po aktivaci katalyzátoru byly provedeny experimenty, které se zaměřovaly na teplotu náběhu katalyzátoru, pracovní teploty katalyzátoru/oleje a závislosti tvorby methanu na teplotě, respektive ideální teplotní okno, při kterém bude nejvyšší konverze oxidu uhličitého. Dále byl proveden experiment zaměřený na dlouhodobou stabilitu katalyzátoru a také bylo testováno chování katalyzátoru při náhlém odstavení jednotky. Pro všechny experimenty byl použit modelový bioplyn s vodíkem viz tabulka 2.
Označení | Složení vstupního plynu [obj. %] | Poměr H2/CO2 | Poměr CH4/CO2 | Průtok [l/hod] |
---|---|---|---|---|
1 | CH4 – 23,1 %; CO2 – 15,4 %; H2 – 61,5 % | 4:1 | 60:40 | 650 |
První experiment s katalyzátorem na bázi niklu se zabýval teplotou náběhu katalyzátoru. V prvním kroku byl reaktor s katalyzátorem v atmosféře vodíku zahříván. Po dosažení teploty 160 °C byl do reaktoru vpuštěn modelový plyn a reaktor byl dále ohříván, než došlo k nastartování reakce. Katalyzátor Ni/CeO2-y-Al2O3 nastartoval reakci při 200 °C v reaktoru (teplota oleje při nájezdu 235 °C).
Druhý experiment se zaměřoval na zjištění katalytické aktivity katalyzátoru. V prvním kroku byl reaktor s katalyzátorem v atmosféře vodíku zahříván. Po dosažení teploty 160 °C byl do reaktoru vpuštěn modelový plyn a reaktor byl dále ohříván, než došlo k nastartování reakce. Po nastartování reakce byla teplota oleje snížena na 200 °C a sledován průběh reakce. Současně byl odebírán produkt a on-line analyzován pomocí analyzátoru Sewerin Multitec 540. Nejvyšší produkce methanu ve výstupním plynu 89 mol. % byla naměřena při teplotě v reaktoru 550 °C. Výsledky tohoto experimentu znázorňuje obr. 11.
Posledním experimentem byl dlouhodobý experiment o délce 500 hodin, který se zaměřoval na dlouhodobou stabilitu katalyzátoru. Výsledek experimentu je znázorněn na obr. 12. Pokles konverze oxidu uhličitého po 500 hodinách na katalyzátoru Ni/CeO2-Al2O3 byl z 93,9 % na 93,6 %, čímž se prokázalo, že přídavek ceru zvyšuje dlouhodobou stabilitu katalyzátoru (v porovnáním s již dříve vyvinutým katalyzátorem bez přídavku ceru do nosiče – Ni/Al2O3).
Závěr
Článek se zabývá vývojem zařízením pro produkci RNG z BRO. Cílem projektu je za prvé vývoj zařízení na přeměnu BRO na bioplyn, za druhé vývoj methanizačního zařízení a katalyzátoru uzpůsobeného pro využití bioplynu, jako zdroje oxidu uhličitého a za třetí finální termochemické zpracování odpadu z anaerobního fermentoru. Projekt má tedy tři hlavní cíle – vývoj a konstrukci zařízení na zpracování BRO s ohledem na efektivitu anaerobního procesu, vývoj methanizačního zařízení pro přeměnu bioplynu na RNG a konečné termochemické zpracování BRO (hygienizace, sušení a pražení).
Zaměření tohoto článku je na methanizační zařízení a na testování vyvinutého katalyzátoru. Katalyzátor byl otestován na modelovém bioplynu, který obsahoval 60 obj. % CH4 a 40 obj. % CO2. Nejvyšší produkce methanu 89 mol. % byla dosažena při teplotě 550 °C v reaktoru a teplotě chladícího oleje jen 200 °C. Katalyzátor byl dále podroben dlouhodobému experimentu, který se zaměřoval na stabilitu katalyzátoru po dobu 500 hodin. Při tomto experimentu byl zaznamenám pokles konverze oxidu uhličitého z 93,9 % na 93,6 %, čímž se prokázalo, že přídavek ceru zvyšuje dlouhodobou stabilitu katalyzátoru.
Poděkování
Tento výstup vznikl v rámci projektu Specifického vysokoškolského výzkumu – grant No. A1_FTOP_2022_005 a dále byl realizován za finanční podpory TAČR – Trend projekt FW01010461 (Vývoj zařízení maximalizující využití BRO při přeměně na bioplyn s využitím katalyzátoru na konverzi CO2 a následného termochemického zpracování odpadního materiálu).
Literatura
- Roční zpráva o provozu elektrizační soustavy ČR – https://ipodpora.odbory.info/soubory/uploads/eruelektro2021.pdf
- BIOM.cz – https://biom.cz/upload/6e01d6d4c4835ec93cda508772f3bf6e/bioplyn.pdf
- Hlinčík T., Tenkrát D., Šnajdrová V., Baraj E.; KATALYTICKÁ METHANIZACE BIOPLYNU S POUŽITÍM NIKLOVÉHO KATALYZÁTORU, Paliva, 2017
- AWE, Olumide Wesley, et al. A review of biogas utilisation, purification and upgrading technologies. Waste and Biomass Valorization, 2017, 8: 267-283.
- europeanbiogas.eu/ –
https://www.europeanbiogas.eu/wp-content/uploads/2022/01/GIE_EBA_BIO_2021_A0_FULL_3D_253_online.pdf - Čermáková J., Tenkrát D.; VYUŽITÍ BIOPLYNU A BIOMETHANU, Paliva, 2010
- Rönsch S., Schneider J., Matthischke S, Schlüter M., Götz M., Lefebvre J., Prabhakaran P., Bajohr S.; Review on methanation – From fundamentals to current projects, Fuel, 2015
- IMAO.sk – https://www.imao.sk/bioplynove-stanice/
- https://ekonomickydenik.cz/alternativa-k-dovezenemu-zemnimu-plynu-treti-bioplynka-v-cesku-zacala-vyrabet-biometan/
- Česká bioplynová asociace – https://www.czba.cz/mapa-bioplynovych-stanic.html
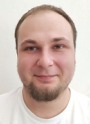
Ing. Jan Kulas (*1992)
Je výzkumným pracovníkem v oddělení Vodíkových technologií ÚJV Řež, a. s., a doktorandem na Ústavu plynných a pevných paliv a ochrany prostředí, VŠCHT Praha. Ve své disertační práci se zabývá využitím katalytické methanizace bioplynu.
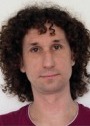
Ing. Lukáš Polák, Ph.D. (*1982)
Absolvent Ústavu plynárenství, koksochemie a ochrany ovzduší na VŠCHT Praha, od roku 2011 pracovník vědy a výzkumu v oddělení Vodíkových technologií ÚJV Řež, a. s., kde se zabývá využitím vodíku v dopravě a jeho potenciálu pro akumulaci energie.
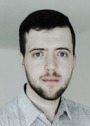
Nikita Streltsov (*1993)
Absolvent oboru Energetika a Procesní technika na ústavu procesní a zpracovatelské techniky fakulty strojní ČVUT v Praze. Je zaměstnán v ÚJV Řež, a. s. na oddělení Vodíkové technologie a inovace v energetice.
Catalytic methanization of carbon dioxide increases the content of sustainable biomethane, or RNG (Renewable natural gas), produced from BRO (biodegradable waste). The advantage is the production of biomethane (increase in energy content) without the need for carbon dioxide separation.